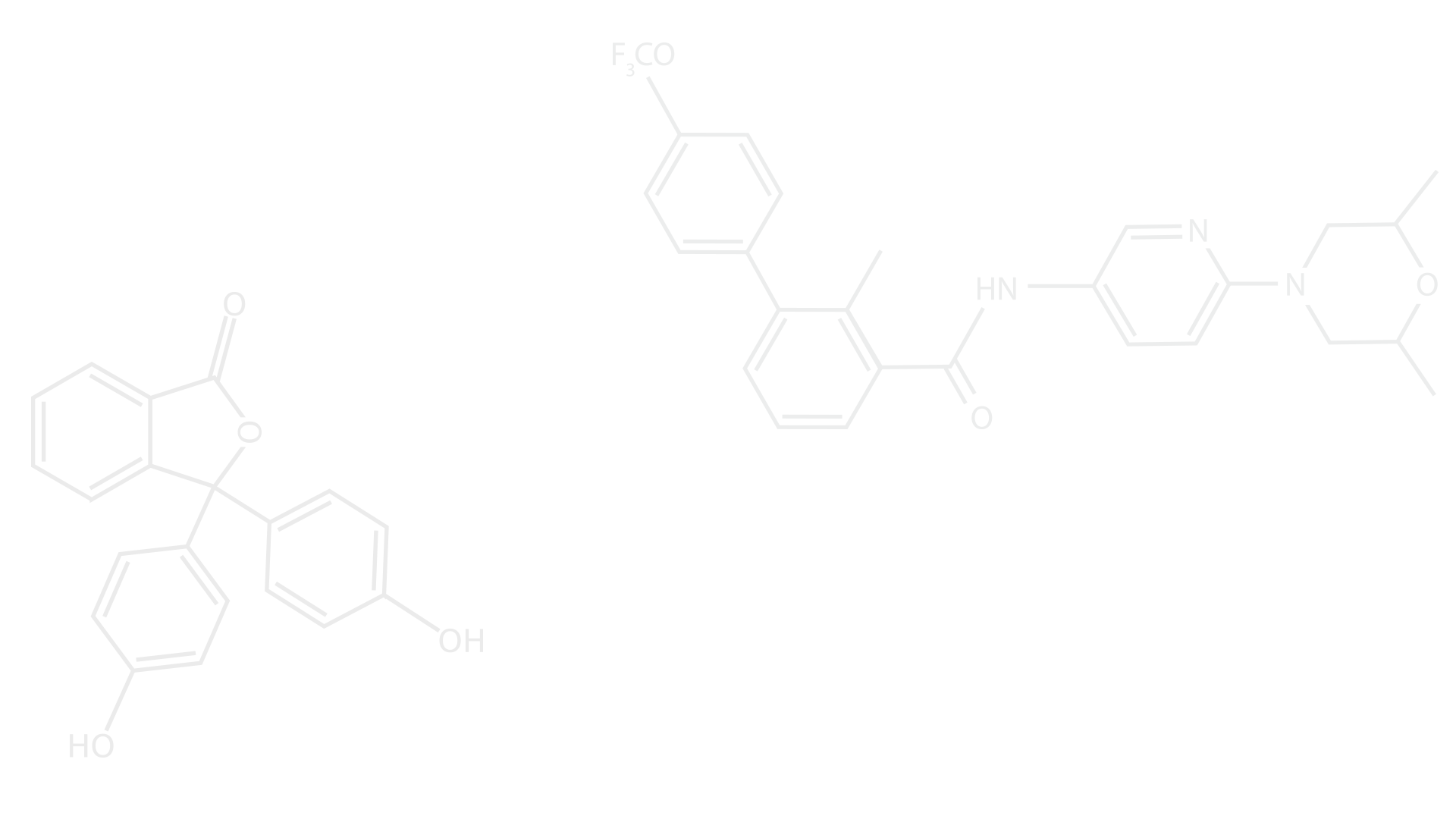
CURRENT RESEARCH
Our current research is built around multi-purpose, multi-physics materials—coal-derived graphene and high porosity aluminum and graphene foams.
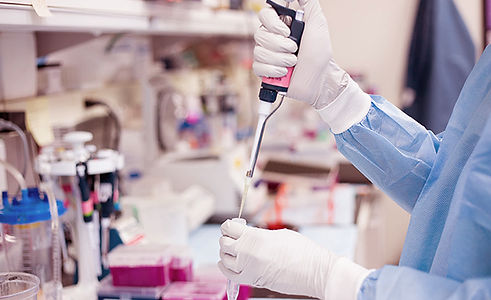
Scalable, cost-effective, one-pot production of graphene from coal
In recent years, graphene has emerged as a wonder material in the field of composite materials and devices due to its unique physical and chemical properties. As a single layer of graphite, graphene features a perfect two‐dimensional (2‐D) structure with large specific surface area (theoretical = 2630 m 2 g ‐1 ), high intrinsic carrier mobility (200,000 cm 2 v ‐1 s ‐1 ), strong mechanical strength (Young’s modulus of ~1.0 TPa) and superior flexibility. But the existing methods to synthesize graphene and its derivatives are mostly suffer with high cost, low production (e.g. time consuming and based on the use of harsh reactants, metal catalysts or ultrasonication). In this scenario, either a scalable and practical production method for graphenic structures with good opical/electrical properties or an identification of cheap sources other than graphite is challenging. If successful, this would advance the industrial applications of graphenic materials even more rapidly. Among several methods, Hummers method, a top-down technique, is considered among the most promising for graphene mass production. It produces a single or a few layers graphene nanoflakes from graphite (natural or synthetic) by chemical and
mechanical exfoliation. However, this method has several limitations. First, natural graphite is a limited resource due to regional localization around the world. China has dominated natural graphite, supplying up to 80% of the world’s production. The price of natural graphite has more than doubled over the past few years ($1,800/ton, 2013). Synthetic graphite is very expensive to produce, because it is prepared from pre- graphitizable carbons like petroleum byproducts at high temperatures close to 3000 °C. Second, conversion of graphite to graphene oxide (GO) followed by reduction
from GO to graphene comprises of multiple steps and excessive use of strong acids and oxidants as well as high-energy consumption. If we want to fully exploit the rather exceptional properties of graphene for large scale deployment covering a broad spectrum of applications, we need to develop alternative techniques that use less expensive carbon sources, chemicals and energy. To meet this need, we propose using coal as a precursor for graphene and novel synthesis technique to convert this inexpensive raw material to graphene oxide to graphene.
The focus point of this project is to develop a simplified, scalable, and cost-effective route to prepare graphene and its derivatives from coal.
Designing non-noble catalysts for electrochemical hydrogen production
Hydrogen (H 2 ) is widely regarded as an attractive alternative to carbon-based fuels in future energy system with the benefits of high energy density and zero pollution. H 2 can be generated from diverse resources, including water, biomass, natural gas, or (after gasification) coal. Currently, around 95% of the world’s total H 2 production is achieved by steam reforming natural gas or other fossil fuels, which requires high temperature and pressures. Furthermore, the produced H 2 by this pathway will be unavoidably contaminated by a high concentration of carbon monoxide (CO), which affects the purity of H 2 and also poisons catalysts during operation. More importantly, production of H 2 by steam reforming still cannot relieve dependencies on legacy fossil sources or reduce the coproduction and release of pollutants. Water electrolysis can provide a promising alternative avenue for ultra-pure H 2 production. The electrolysis of water is to produce H 2 and O 2 gas at cathode and anode, respectively. At standard temperature pressure, the thermodynamic decomposition voltage of water in theoretical condition is 1.23 V, corresponding to an energy input of ~G=237.2 kJ mol -1 , and the current efficiency is 100%. Unfortunately, the sluggish kinetics of both hydrogen evolution reaction (HER) at the cathode and oxygen evolution reaction (OER) at the anode require high overpotentials to yield appreciable current densities. Hence the practical energy consumption in practical electrolyzers is nearly 1.5 to 2.2 times more than the theoretical energy consumption, with the actual efficiency is only between 48% and 70% in current commercial electrolyzers. To address the challenges in conventional water electrolysis modes, several strategies, focusing on various aspects such as electrolyte membrane technology, electrocatalyst engineering, and electrolyzer design, have been proposed. In this project, we focus on electrocatalyst engineering.
The focus point of this project is scalable production of cost-effective eletrocatalyst for efficient hydrogen production. In this project, our designed Nb-based nano-flowers could generate 1 A/cm 2 of current density at as low as 300 mV overpotential.
Electrocatalysts for metal-air batteries
Metal-air batteries are a promising technology to deal with future energy demands by virtue of their high theoretical energy density (up to 11,000 Wh kg −1 for Li-air battery), low price, eco-friendly nature, and safety. However, metal-air batteries in demonstrative energy devices have not been proved efficient in generating a promising output due to the poor cyclic stability resulting from the sluggish kinetics of oxygen reactions and weak durability of catalysts at the air-cathode. To overcome these
deficiencies, we need to investigate oxygen-reduction reaction (ORR) and oxygen- evolution reaction (OER)—the two significant processes in rechargeable metal-air batteries (O 2 + 2H 2 O + 4e − ↔ 4OH − ), with oxygen getting reduced while discharging and the reverse process occurring during charging. Efficient bi-functional catalysts that are active for both ORR and OER are one of the major challenges faced in designing rechargeable metal-air batteries. Thus far, the best known catalysts for oxygen electrocatalysis in alkaline media are prohibitive Pt-based metals for ORR and Ir/Ru based metals for OER. However, both of these seriously lack the significant bi-functional property. The development of highly active and stable bi-functional catalysts using economic transition metals is thus an important undertaking for industrial grade metal-air batteries. In this project, we aim to design efficient and cost-effective bi-function catalyst for metal-air batteries. In the first case we have designed oxygen deficient, high aspect ratio perovskite platelets which have high bi-functional activity towards reversible oxygen electrochemistry.
The focus point of this project is to lead the emerging metal-air battery technology to the commercial level. Since metal-air batteries have extremely high energy density and are lightweight because they use oxygen in ambient air as the primary source of fuel. Air cathodes being the prominent part of their design, cost-effective, bifunctional electrocatalysts are the need of hour.
Janus Film Humidity Sensor
Control and sensitive measurement of moisture changes is essential in a wide range of industrial applications. However, conventional humidity sensing mechanisms have limitations in reliable and rapid detection under harsh conditions such as high relative humidity and high temperature. Here, we present a Janus (GO/rGO) film as a humidity sensor that exploits the
extraordinary water uptake and hygroscopic properties of two-dimensional graphene oxide (GO) laminar structure. The proposed sensor has superior hygroscopic properties, including humidity sensitivity, excellent repeatability, and fast response-recovery. The sensor also overcomes the limitation of the currently available complex interdigitated transducer-based humidity sensor. The freestanding Janus GO/reduced GO (rGO) film was successfully fabricated through a novel Al-assisted partial reduction technique combining with low-temperature drop-casting. The self- assembled laminar structure of the Janus film facilitates the diffusion pathway of water molecules efficiently.
Graphene based Structural Composites
*under construction*
Graphene-based TIMs for thermal management
*under construction*
Biocompatibility of Graphene
Titanium implants are well-regarded for their affinity for bone cells adhesion. However, implant infections pose a serious risk to patients, since systemically-administered antibiotic drugs often cannot reach the surfaces of implants where microbial biofilms form. The result is multiple surgeries with a high rate of recurrence and an unacceptable margin of mortality. Graphene Oxide (GO) coatings on such implants and screws can provide inherent antimicrobial properties while providing improved apatite adhesion for safer, longer-lasting implants.